Watch a specimen of Ecballium elaterium for long enough, and it’ll become clear how it gets its other name: the squirting cucumber. When it’s time to reproduce, the fruit performs a piece of magic, turning its pulp into a sticky liquid, which expands inside it, eventually causing it to explode and squirt its seeds a long distance, quickly.
A research team led by Professor Zhang Li from the Department of Mechanical and Automation Engineering of Faculty of Engineering at The Chinese University of Hong Kong (CUHK), with theoretical and methodological advice from Zhejiang University and Carnegie Mellon University, has recently turned to the squirting cucumber as a surprising source of inspiration for a very different task: powering robots – specifically, miniature robots, those about the size of an insect, from a few millimetres to a few centimetres. They have an increasing range of uses, including critical medical tasks inside the human body – but they’re so small, it’s hard to fit them with a sufficiently large power pack, otherwise known as an actuation system.
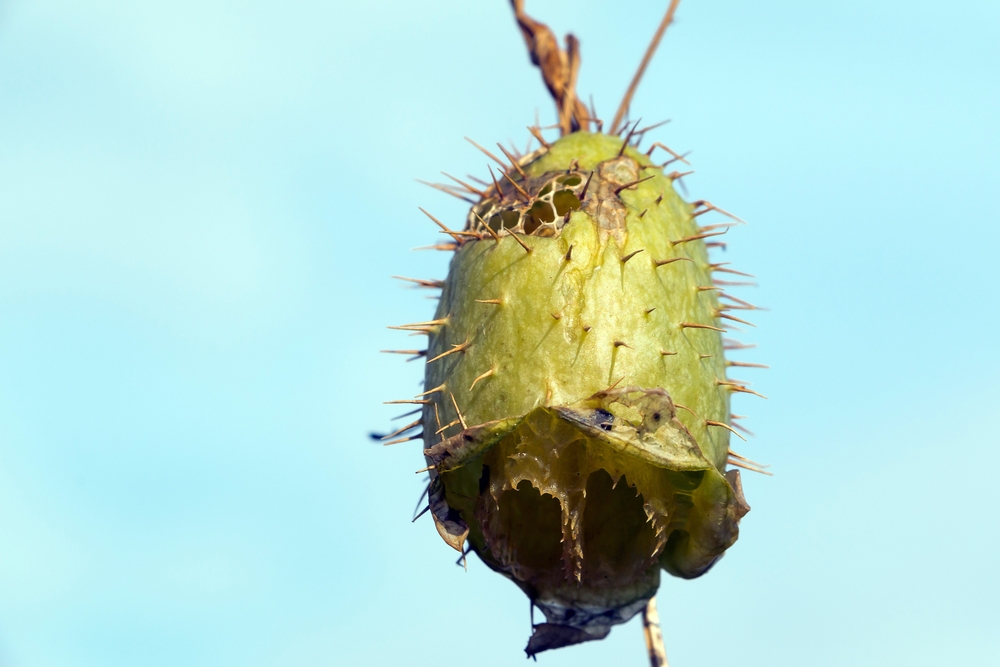
“For robotic tasks that require jumping, ejection or catapulting, such devices typically need energy release over short time durations to produce a sufficient driving force,” says Professor Zhang. “Current miniature robot systems always require sophisticated fabrication processes to integrate multiple components, and usually fall short of the performance of natural systems due to limitations on pre-stored energy.”
Enter the squirting cucumber. Its ingenious method of spreading its seeds gave Professor Zhang and his team the idea to develop the accumulated strain energy-fracture power amplification mechanism (ASEF). The technology works like an archer pulling back a bowstring, storing energy and releasing it all at once for a powerful launch.
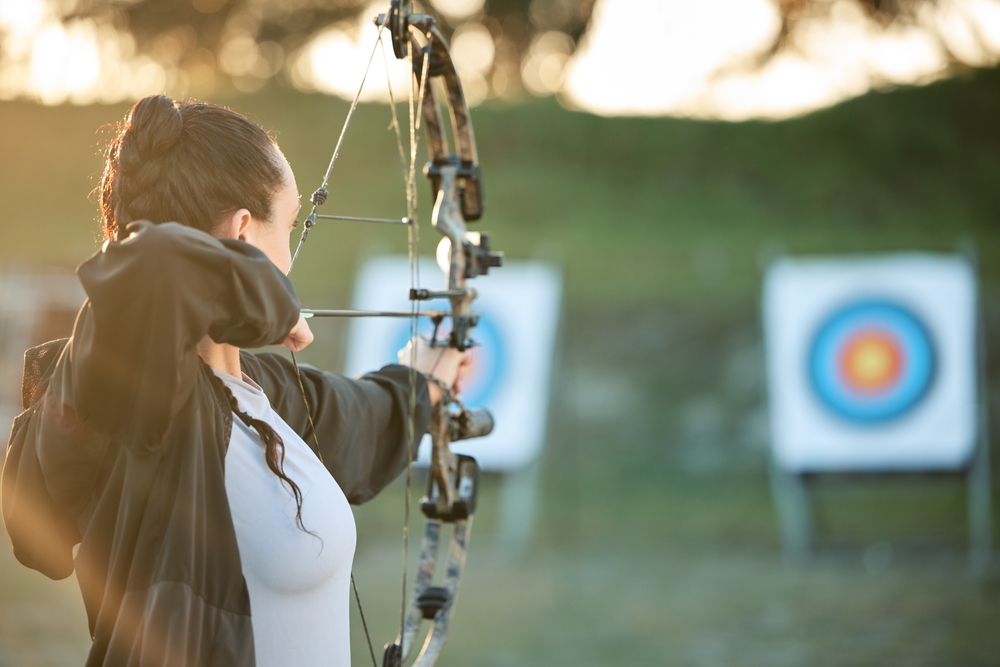
Using a launcher made of hydrogel, a type of material that combines a permeable solid with water, the ASEF system is activated by shining near-infrared light onto it, causing the water to change into vapour, making it expand. Eventually, the bottom of the launcher fractures, much like the squirting cucumber, and fires the launcher over incredible distances: a launcher 7mm wide and 3mm tall can spring over 193 cm vertically, or 643 times its own height, at a speed of about 7.5 m/s and an acceleration is 2,500 times the gravitational acceleration on the Earth surface (2,500 g), hugely outperforming existing systems.
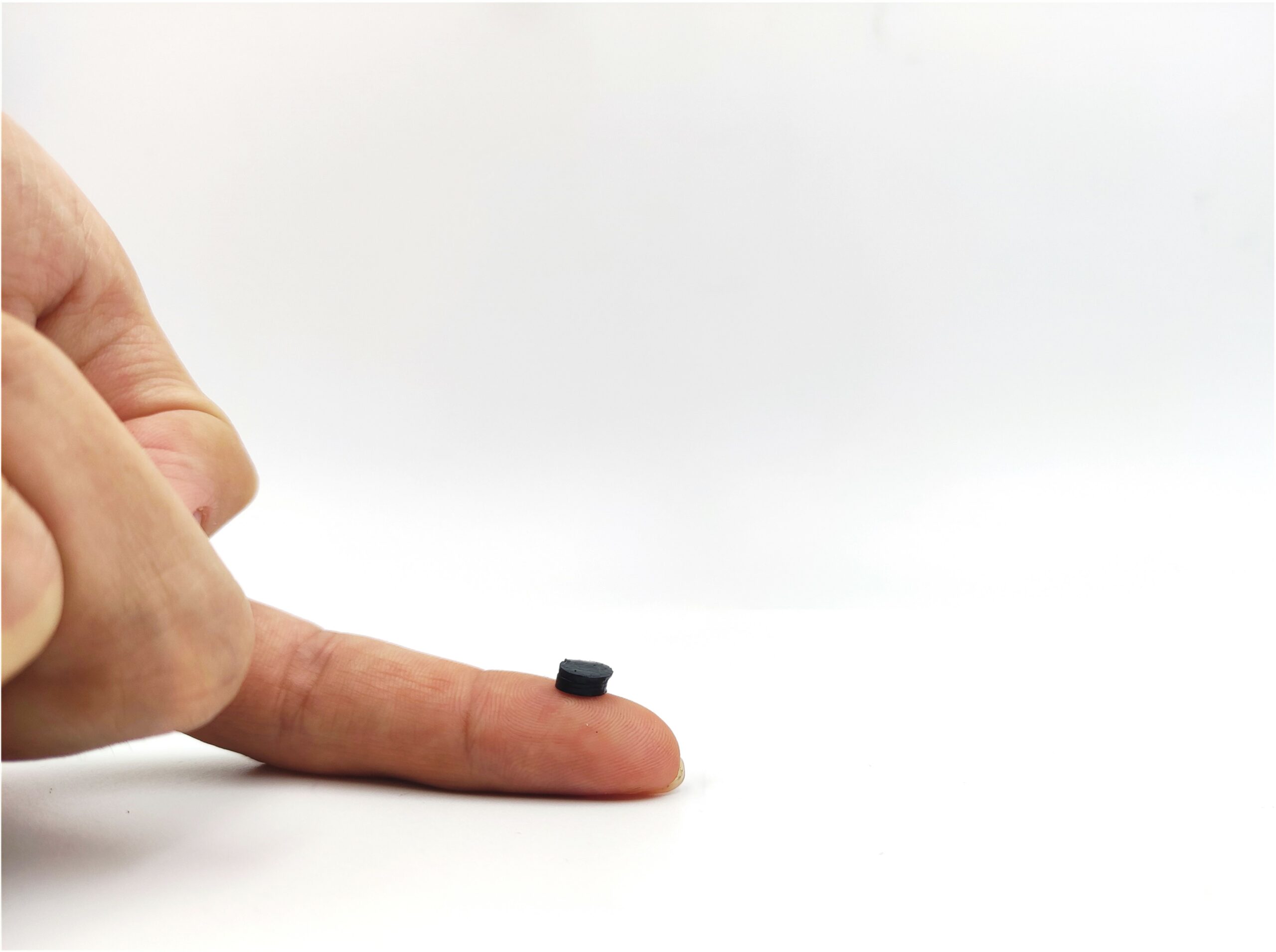
The potential for medical applications is immense: Professor Zhang says it raises the possibility of robots that can venture deep inside the human body to perform therapeutic tasks. Now the launchers can only be used once; the next stage, ahead of commercialising it, is to make reusable ones.
“We are now exploring material innovation and try to do some medical applications, such as stent delivery and expansion, and deep tissue sampling. Although this technology is still in its infancy, we hope to achieve commercialisation and widespread application in the next five years. The biggest obstacle we need to overcome is to achieve repeatable actuation and integrate it into the robot.”
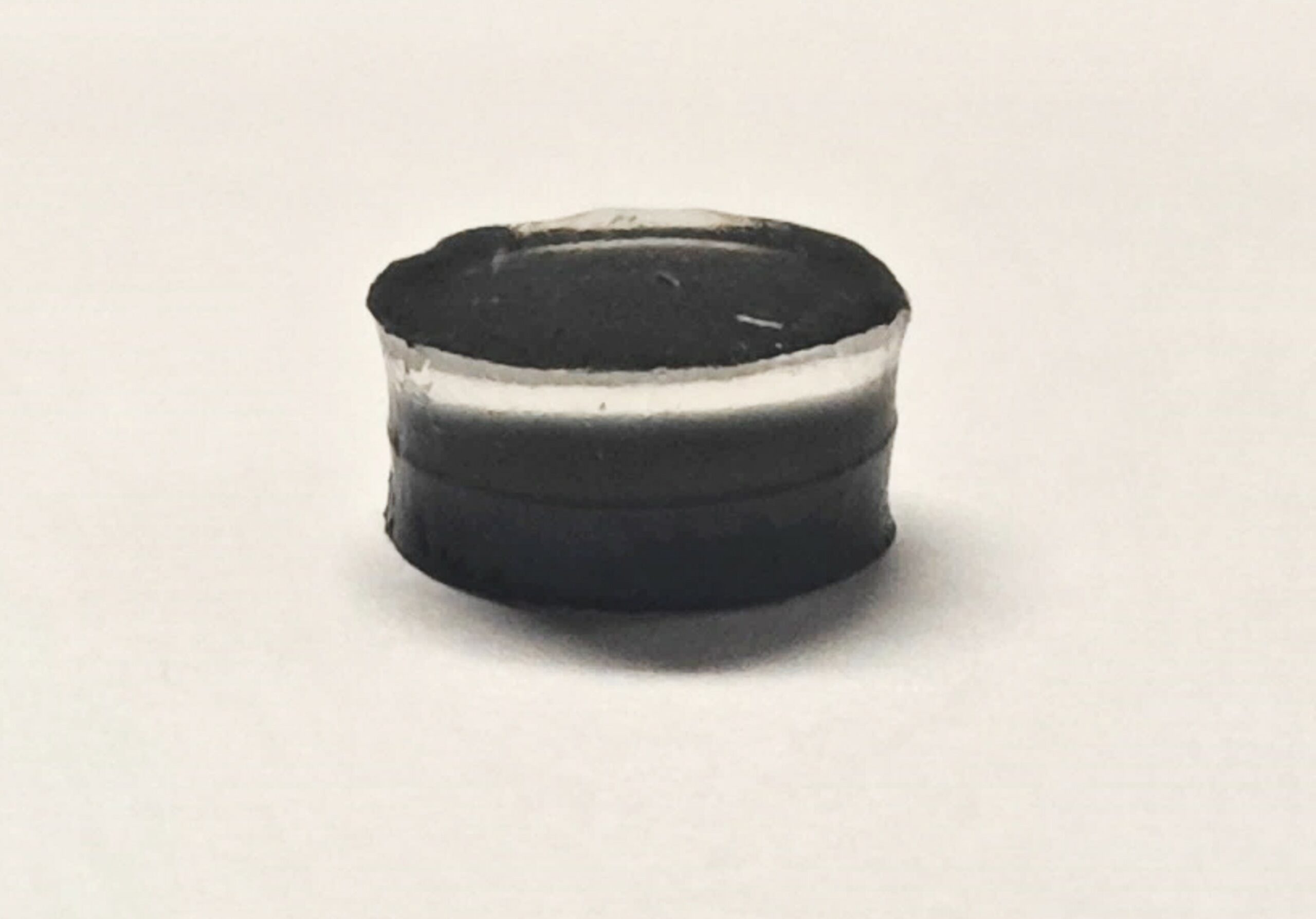
Medicine is not the only area where the new propulsion system could have a seismic impact. The team has also built a prototype of an agricultural robot that can jump long distances and release seeds automatically.
Building brighter bots
Controlling the motion of miniature robots is one thing, but controlling the motion of their even tinier cousins, micro and nano-robots, is an even bigger challenge. With micro machines that can be as small as millionths of a metre or smaller in size, the biggest advantage is their tiny scale, which allows them to easily navigate through and perform tasks in small and complex spaces, but all sorts of things get in the way when it comes to trying to move them around the human body. These include the nature of the robots themselves and how they interact with each other, considerations like the random movements of particles known as Brownian motion, plus the complexities of the human body’s layout and the fluids within it.
“These unquantifiable factors often hinder the effectiveness of traditional control algorithms in achieving the desired motion performance of micro-/nano-robotic systems,” says Dr Jiang Jialin, postdoctoral fellow in CUHK’s Department of Mechanical and Automation Engineering.
In fact, they’re so complicated that traditional computational methods struggle to process them. Professor Zhang and the team are looking to crack this particular code using the power of machine learning. They recently published a review paper about the exciting ways in which the technology can make it quicker to develop micro-/nano-robots, as well as making them easier to control and move around. For instance, machine learning can process the incredibly complex images from within the human body to accurately map the robots’ location, and then help them to navigate more accurately.
“Machine learning algorithms can operate without relying on precise models of the target systems,” says Dr Jiang, who is one of the authors of the paper. “Through extensive and effective training, they can autonomously induce and synthesise control strategies. Compared to traditional methods, they can significantly simplify the design process of control systems.”
By harnessing the power of machine learning, these micro and nano-robots can autonomously navigate complex human anatomical structures, delivering treatments with precision that was previously unattainable. This technological leap could possibly improve patient outcomes and reduce the risks associated with traditional surgical interventions, ushering in a new era of minimally invasive, targeted medical therapies.
For more detailed information, please refer to the full study:
Fracture-driven power amplification in a hydrogel launcher | Nature Materials
Machine learning for micro- and nanorobots | Nature Machine Intelligence